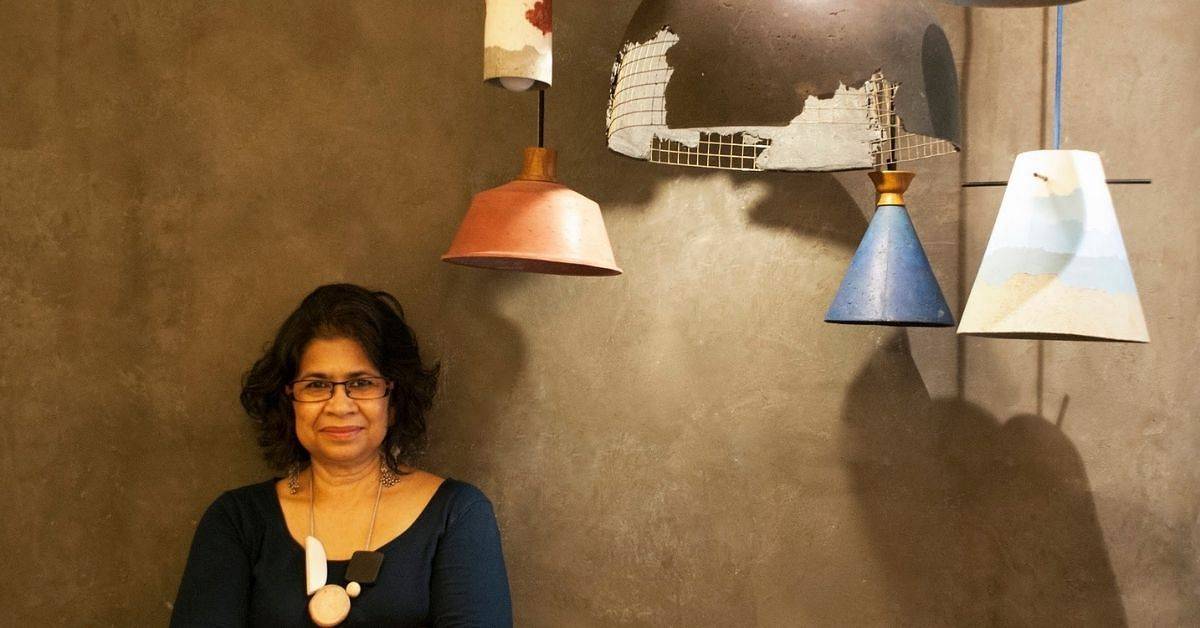
Jenny Pinto's decision to quit the film business in the 1990s was a radical move in more ways than one. The leave meant bidding adieu to the exhilaration of a fast-paced life as an ad filmmaker and welcome to the ups and downs of revolutionizing an industry that was, back then, yet untapped.
"I grew up in Mumbai and began my career there. It was a really exciting time to be in advertising just before liberalisation," she said.
But, as she approached parenthood, she began to doubt consumerism and its influence on the environment. "I started thinking about how I wanted to raise my child and what type of society she would grow up in," she says. It was time to make the switch to greener living, even though she wasn't sure how she'd achieve it.
Jenny's new life and profession would go on to become a pioneering force in India's sustainable paper and lighting sector, something no one could have predicted. Today, her homegrown company Oorjaa sells products ranging from elegant lighting to creative home accessories, all made from recycled materials.
For and from the environment
Jenny describes her experiment with paper-making as "accidental discovery."
"I left Mumbai in my mid-30s to resettle in Bengaluru and see what I could do to investigate the environment from a more behavioural aspect. I was there learning pottery when I came upon a lec-dem (lecture-demonstration) on handmade paper," she adds.
One thing led to another, and by 1998, her passion had grown sufficiently to open a small studio, one of the first in India, to master the art of papermaking via trial and error.
According to the 2011 census, the utilisation of waste materials in the production of green paper recovers just 27% of waste paper and 22% of agricultural waste. These figures were even grimmer a decade before that.
Jenny chose to learn how to produce recycled paper from agricultural waste for a cleaner society against this backdrop.
"No one was manufacturing paper on a small scale in India in this way, that is, chemical-free, made from banana fibre, and transparent enough for lighting. However, I discovered many such ventures in the United States," she says.
She spent a few months in Portland in 2000, working with Helen Hiebert on natural fibre paper and lighting.
Jenny feels that making paper is not difficult, but making it green takes particular consideration.
"Because paper is created from plant cellulose, so it is a natural material. The variables in this situation are the source of the material and the technique of extraction and production," she adds, adding that the process entails cooking the fibre in water and additives and lofting the pulp on moulds.
Knowing that the operation was water-intensive, she put up a rainwater harvesting and water recycling unit so that all water from the paper-making process could be recycled and utilised in the garden. "I usually utilise less harmful compounds in the manufacturing. For example, instead of caustic soda, the fibres are cooked in washing soda," she says. As a result, the paper may be recycled and securely composted after use.
Woman with a new trend
While she mastered the complex procedure, scaling it up posed its own plethora of challenges. Jenny had to persuade machine makers to supply small-sized equipment when she first started out. An innovative approach meant a scarcity of skilled people to form a team. She also needed to identify suppliers of agri-waste, such as banana fibre.
"I identified a couple manufacturers who agreed to construct a small beater and press for my production. Finding banana fibre, my major raw material, took some effort as well, but I eventually discovered it being extracted for the craft industry," she reveals.
Convincing people to believe that paper is robust enough material for interior decoration was a tough nut to crack in itself. To tackle this, she used on-site exhibitions to communicate with her audience about the topic.
"There was also a rising group of architects who were exposed to foreign designers like Isamu Noguchi and Ingo Maurer, who had previously utilised paper in lighting wonderfully, so one learnt to negotiate" she adds.
Oorjaa has established itself as a renowned fixture in the lighting and décor business. Fatty Bao, Yazu, Gonative, Linkedin, Google, and Reliance are just a few of the initiatives across hospitality and corporate sectors.
Jenny identified potential close to home. Rural artisans from the east who had settled in Bengaluru were noted for their deftness with handicrafts. They were fast to pick up new skills and loved working with natural materials. "These folks came to us looking for employment and stayed with us for years," she adds. Jenny now has around 50 men and women working for her after she personally taught them.
Oorjaa Brand
Her goods evolved into a full-fledged homegrown brand named Oorjaa in 2018. Jenny's work as a lighting designer with an emphasis on sustainable materials drew the entrepreneurial knack of Radeesh Shetty, who provided funding for development.
"We used raw materials such as faux cement produced from quarry waste and cork made from discarded industrial cork. Our most recent material is lantana camara, which is now seen as a major threat to forests and animals in central and southern India," she reveals.
Their goal remains to repurpose and recycle anything that can be used or recycled. "After smashing it, we shape faux cement into lamps, doorknobs, and other decorative items. In the papermaking process, water is recycled wherever feasible. The woven papers are used to make several types of lamps. The remaining cork is used to make coasters and other goods," she explains.
Jenny has watched people grow more concerned about what is created and how it is made when she first started out. "More and more consumers are concerned about where they source their products from. It's sometimes a part of the tender for certain architectural projects, and they prefer locally made products," she reveals.