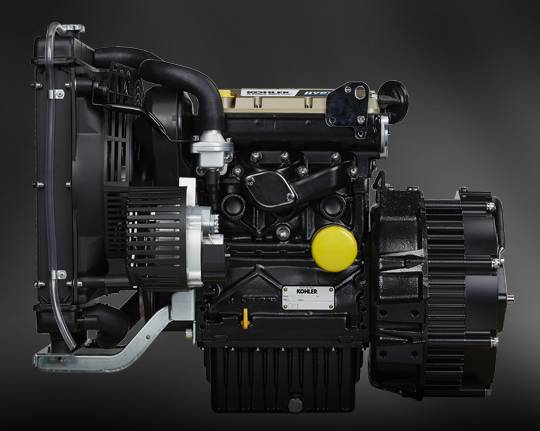
EIMA International Expo 2018 was held from 7th to 11th November 2018 in Bologna, Italy. The event exhibits products such as Agriculture Processing Machinery, Weighing & Harvesting Machinery, Chemical Fertilizing & Spraying Equipment, Grain Processing Machinery, Crop Cleaning, Grading, Industrial Feed Stuff Production, Irrigation Systems & Equipment etc. used in the Agriculture and Forestry sector.
Kohler Co. displayed the K-HEM (KOHLER Hybrid Energy Module) hybrid electrical and mechanical combined power generation unit at EIMA International 2018. In light of the changes that the new emissions directive will bring to the off-road applications sector beginning on 1 January 2019, Kohler has added a product to its array that is capable of meeting the new needs of equipment manufacturers in this sector.
A variety of energy sources are available on the market. Rather than investigate their different applications and individual characteristics in order to set them up in competition with each other, Kohler has chosen to integrate them, to pair them with each other, so as to reap all of their potential value.
This is the philosophy behind K-HEM, the unit that generates power using a combination of a KDW 1003 18-kW diesel engine, compliant with Stage V standards and without DPF, and a 48-volt electric engine that guarantees 15 kW of peak power and 9 kW of continuous power. This means that the unit is capable of providing over 30 kW without the need for exhaust gas after treatment systems. Moreover, K-HEM can operate as a generator for energy accumulation systems.
The features that the K-HEM hybrid unit offers have been designed to satisfy the needs of all those types of equipment that are distinguished by intermittent duty operation cycles that call for power peaks (welders, mowers, tractors with implements, etc.) and machines that chiefly run continuous low load operation cycles, which prevent them from reaching the temperatures necessary for passive regeneration to occur inside the particulate filter (aerial platforms, forklifts, etc.).
With K-HEM, the power base is provided by the combustion engine, while the power peaks are guaranteed by the electric engine. This system, which complies with the limits laid down in Stage 5 standards, makes it possible for machines to avoid derating and guarantees high productivity levels. Indeed, the built-in master control unit allows users to monitor and manage working modes and transitions based on their needs.
Salient features
Greater efficiency- The diesel engine guarantees maximum performance in specific operating conditions. This means that the hybrid unit makes it possible to achieve optimal operating points more rapidly and more frequently, thereby increasing the efficiency of the operations performed and, consequently, the equipment’s productivity.
Recovery operations- Thanks to the dual function of the electric component, which works both as a generator and as an auxiliary engine, it is possible to recover energy from the transmission system during the machine’s braking and exhaust phases and from the combustion engine itself during operating phases with low energy demands. The energy stored in the battery will thus be available when the machine requires more than the threshold of 18 thermal kW of installed power, exceeding even 30 kW. This translates into considerable savings in terms of emissions, consumption and installed thermal power.
Perfect integration - Equipment manufacturers do not need to worry about possible
installation problems, given that the hybrid unit can be integrated into a hydraulic system or a mechanical transmission, in the same way as a diesel engine.
Precise management - The high degree of integration between the mechanical and
hydraulic parts that the hybrid unit allows makes it possible to completely optimise machine management: each actuator can be managed by the hydraulic or electrical system depending on specific requirements, and controlled by the master control unit that oversees the system. The most striking example is that of agricultural attachments: the ability to disengage them from the mechanical system and manage them using the electrical system now allows for exceptional optimisation of operations.
About Kohler Engines
Kohler began manufacturing engines more than 90 years ago and has continually enhanced its product line-up in an effort to help make life easier and more profitable for end users around the globe. Today, the company offers a full array of diesel, gasoline and gaseous-fuelled engines – up to 140 hp. – which are supplied to equipment manufacturers worldwide in the construction, agricultural, industrial and lawn and garden markets.
About Kohler Co.
Founded in 1873 and headquartered in Kohler, Wis. Kohler Co. is one of America’s oldest and largest privately held companies. With more than 50 manufacturing locations worldwide, Kohler is a global leader in the manufacture of engines and power systems; kitchen and bath products; and owner/operator of two of the world’s finest five-star hospitality and golf resort destinations in Kohler and St Andrews, Scotland.
For more information or details
Visit Kohler.com.
Or contact
Tommaso Maria Vezzosi
Tel: +39 0522 389471
Email: [email protected]
Website: kohlerengines.com/eu
Press Office:
Giacomo Galli
Tel: +39 02 87399276
Email: [email protected]
Website: www.sillabariopress.it